Turbocharger
Used to generate increased engine power and made from heat resistant stainless steels, turbochargers are complex and difficult components to machine. They require sophisticated, custom tools such as high precision reamers and dedicated carbide grades. Processing includes tight-tolerance holemaking and generating superior surface finishes.
YOUR MANUFACTURING CHALLENGES:
- Minimising tool cost per piece when productively drilling numerous holes.
- Reaming precise holes with perfect surface finishes.
- Ensuring high productivity during turning of the outer diameter and face.
- Copying the back profile with high productivity and reliability.
- Roughing component faces with the highest possible productivity and reliability.
- Minimising cycle time and maintaining reliability for grooving operations.
- Efficiently and securely turning the internal diameter and face.
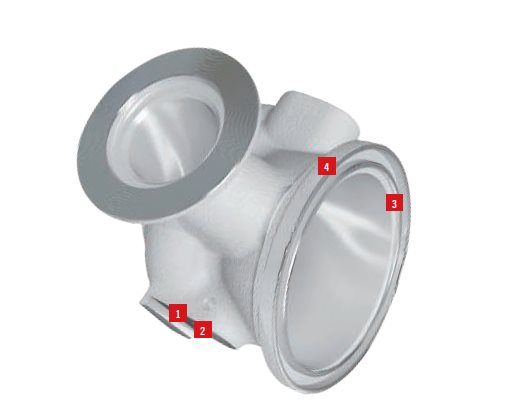
| 1 - Drilling numerous holes |
Your Challenge: | | Minimising tool cost per piece when productively drilling numerous holes. |
Our Solution: | | With strong indexable inserts and a highly stable, low-friction coated drill body, Perfomax achieves excellent productivity and economic performance. The drills feature optimized geometries to eliminate deflection and provide high chip evacuation. Your benefits include increasing throughput and minimising tool cost per part. |
Product: | | PerfomaxTM Drill |
2 - Reaming precise holes
Your Challenge: | | Reaming precise holes with perfect surface finishes. |
Our Solution: | | An interchangeable head reamer, Precimaster™ Plus minimizes cost per hole while providing excellent results. Additionally, our Nanofix™, Precifix™ and Xfix™ lines fill out our range of reaming products, guaranteeing a productive and high quality solution for holes ranging from 2.97 mm to 155 mm in diameter. Your benefits include reducing costs while maintaining exacting tolerances and surface finish requirements. |
Product: | | Seco Reaming Solutions |
3 - Turning the outer diameter and face
Your Challenge: | | Ensuring high productivity during turning of the outer diameter and face. |
Our Solution: | | The flexible Seco-Capto quick change turning head system reduces tool change times and can be error-proof modified for mass production applications. Offering highly rigid and accurate performance, the system also enables full automation of presetting by adding electronic data chips to the tool holders. Additionally, using ISO/ANSI Duratomic® inserts maximizes chip removal rate for this application. Your benefits include reliable accuracy and increased efficiency. |
Product: | | Seco-CaptoTM Turning Tool |
4 - Copying the back profile
Your Challenge: | | Copying the back profile with high productivity and reliability. |
Our Solution: | | The flexible Seco-Capto quick change turning head system reduces tool change times and can be error-proof modified for mass production applications. Offering highly rigid and accurate performance, the system also enables full automation of presetting by adding electronic data chips to the tool holders. Additionally, applying MDT coated inserts maximizes chip removal rate for this application. Your benefits include reliable accuracy and increased efficiency. |
Product: | | Seco-CaptoTM Turning Tool |
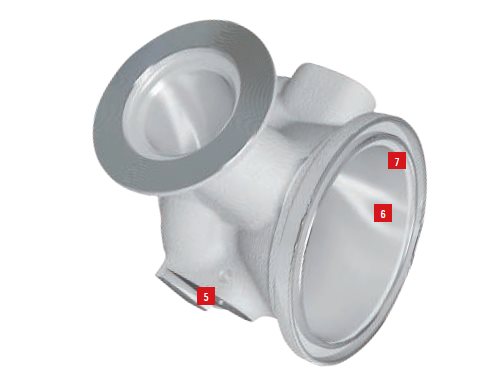
| 5 - Roughing component faces |
Your Challenge: | | Roughing component faces with the highest possible productivity and reliability. |
Our Solution: | | With features perfect for the challenges faced in rough milling turbochargers, the R220.29 copy milling cutter incorporates carbide inserts with strong cutting edges. Round inserts maximize process security and stability, as well as offering improved cost performance by allowing the use of more insert edges. Your benefits include a highly reliable process with minimal cycle times and costs. |
Product: | | R220.29 Copy Milling Cutter |
6 - Minimising cycle time
Your Challenge: | | Minimising cycle time and maintaining reliability for grooving operations. |
Our Solution: | | With a top clamp and serrated contact surfaces between the insert and tool holder, Secoloc insert clamping provides the MDT system with superb stability, which is then further enhanced through the use of long inserts. The Seco-Capto interface adds tremendous flexibility, and the ability to move to full automation by adding electronic data chips to the tool holders. MDT coated carbide inserts optimize chip removal rates in this application. Your benefits include robust performance, high process security and shorter cycle times. |
Product: | | Seco-CaptoTM MDT Axial Grooving Tool |
7 - Turning the internal diameter and face
Your Challenge: | | Efficiently and securely turning the internal diameter and face. |
Our Solution: | | The flexible Seco-Capto quick change turning head system reduces tool change times and can be error-proof modified for mass production applications. Offering highly rigid and accurate performance, the system also en-ables full automation of presetting by adding electronic data chips to the toolholders. Additionally, applying ISO/ ANSI Duratomic® inserts maximizes chip removal rate for this application. Your benefits include reliable accuracy and increased efficiency. |
Product: | | Seco-CaptoTM Boring Tool |